How to Avoid Costly ERP Implementation Pitfalls: The Power of ERP Selection & Requirements Gathering specifically for Manufacturing companies
GP Manufacturing to BC Analysis
When embarking on an ERP project, especially in the manufacturing space, success hinges on thorough ERP selection and detailed requirements gathering. In this blog post, we explore a real-world scenario involving Microsoft Dynamics GP and Business Central to highlight why running a comprehensive requirements analysis is essential before making any platform decision.

The ERP Implementation Dilemma
Imagine a manufacturing company that recently transitioned from Microsoft Dynamics GP (Great Plains) to Business Central (BC). At a user group meeting, a customer shared that their new BC implementation wasn’t delivering the expected results. Despite a full sales process that included input from partners and sales teams, there was a lingering uncertainty about whether the chosen ERP would truly meet their unique operational needs.
The Critical Role of Requirements Gathering
In our conversation with the customer, we discovered that their specific type of manufacturing operations posed a significant challenge for BC. While the initial analysis suggested a 60% fit between BC and their core business requirements, further examination revealed the following:
- Finance vs. Manufacturing Fit:
The finance module showed only about a 10% difference in requirements alignment, indicating that finance was not the issue. Instead, the manufacturing specifics created the real challenge. - Manufacturing Module Disparity:
When drilling down into the manufacturing requirements, the disparity widened dramatically. BC only achieved a 60% fit, whereas an alternative system (F&SCM) offered up to a 98% fit. That 40% gap in manufacturing capabilities could mean the difference between having an ideal system that drives competitive advantage and relying on workarounds like spreadsheets or third-party integrations.
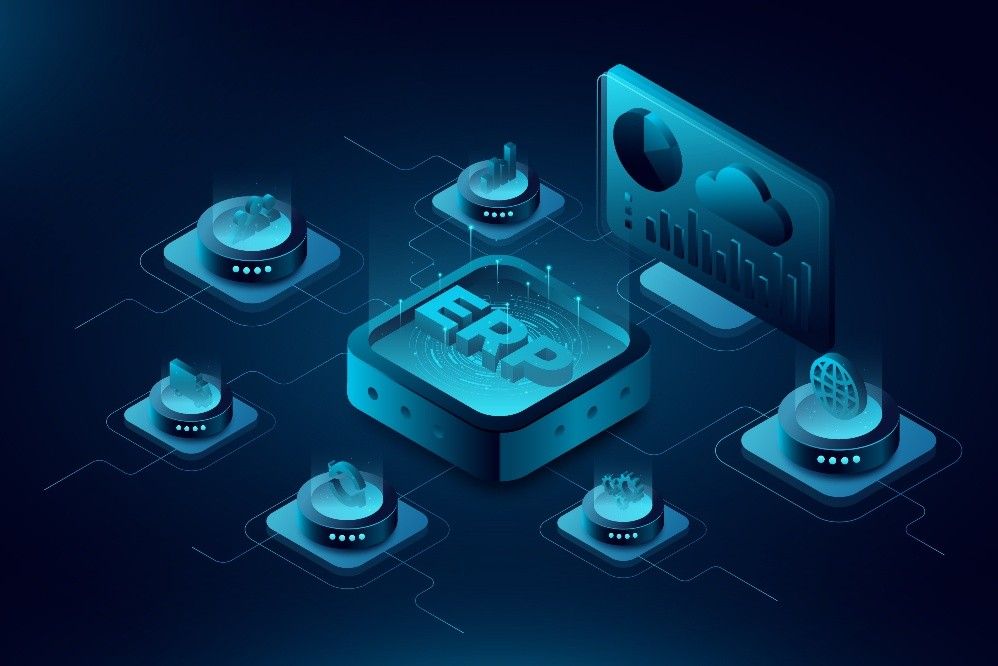
Why ERP Selection Matters
The key takeaway for any manufacturing company—especially those using Great Plains—is to invest time in robust requirements gathering before finalizing an ERP selection. By using an online requirements analysis tool, companies can:
- Identify Critical Gaps:
Understand the exact areas where a proposed ERP system falls short. - Prevent Future Disappointment:
Avoid costly, time-consuming implementations that fail to meet operational needs. - Optimize ROI:
Ensure that the chosen ERP system not only supports current processes but also scales with future business growth.
A Call to Action for Manufacturing Leaders
Before committing to an ERP platform like Microsoft Dynamics Business Central, ask yourself: Have you thoroughly analyzed your core business requirements? An upfront, detailed evaluation of your manufacturing needs can save you a lot of time, money, and heartache in the long run.
Key Takeaways:
- ERP Selection: Choose the right system by carefully analyzing how each ERP solution aligns with your business requirements.
- Requirements Gathering: Leverage tools and expert analysis to pinpoint exactly what your manufacturing operation needs from an ERP solution.
- Avoid Implementation Pitfalls: A proper evaluation process can prevent project failure and ensure your ERP investment drives true competitive advantage.
By prioritizing ERP selection and comprehensive requirements gathering, you position your manufacturing company for a successful ERP implementation that truly supports your business objectives.
Investing in the right approach today means avoiding costly mistakes tomorrow. Take the time to do the analysis first, then decide your direction—your operational efficiency and profitability depend on it.
HandsFree ERP is dedicated to supporting clients with their ERP initiatives, enabling companies to seamlessly connect users with their ERP partners. By utilizing skilled professionals, streamlined processes, and cutting-edge tools, HandsFree ERP significantly boosts the success rates of ERP projects.
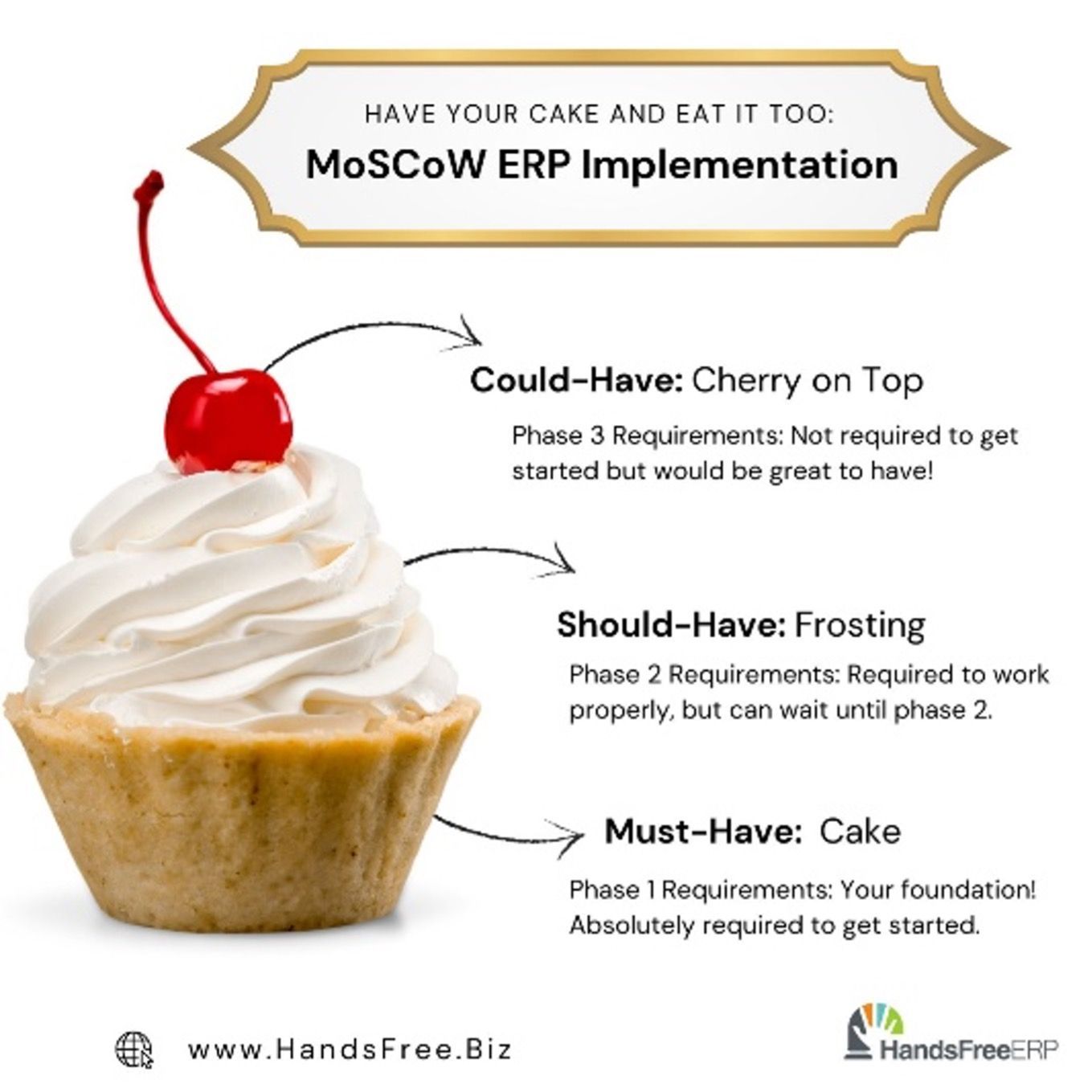